Haitian Precision HPC1000 Horizontal Machining Center
2023-07-06
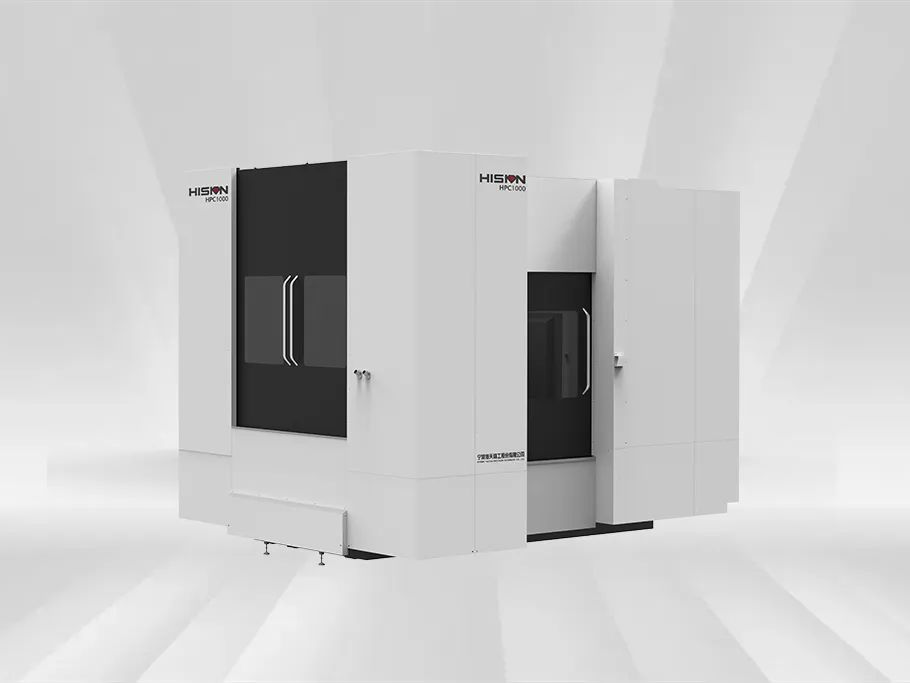
With the rapid development of automobile lightweight, auto parts are integrated from traditional multiple components to single parts, and the processing characteristics of parts are shifted from plane to space, which has spawned many needs for five-axis CNC machine tool processing, where the subframe is an integral part of the front and rear axles, and it is also the skeleton of the axle, which can block vibration and noise and reduce their direct entry into the carriage.
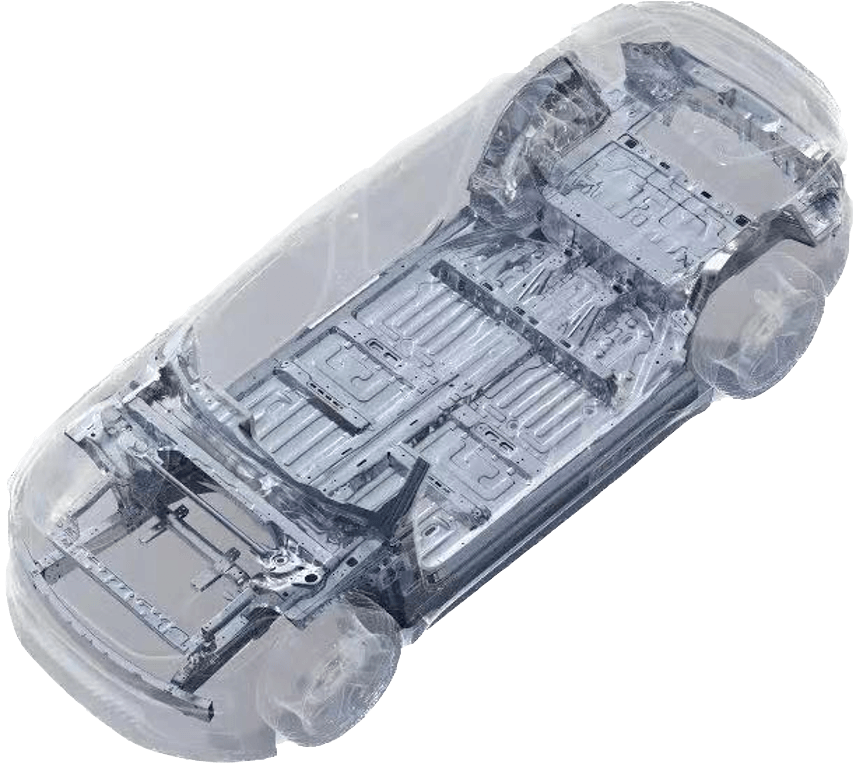
For the workpiece machining of subframes, chassis parts, power battery shells, battery bases, stringers and vibration damping brackets of large-size and slightly complex frames in the automotive industry, a five-axis horizontal machining center with more processing space is required.
Model recommendation
HPC1000 horizontal machining center
The HPC1000 high-speed milling center, suitable for carrying out complex machining of various parts, can automatically exchange tools during machining, and can carry out multi-process machining such as milling, boring, drilling (drilling, expanding and reaming) and tapping threads on multiple sides in one clamping. The compact single table structure provides the most convenient operation of direct loading to the rotary table, which is suitable for small-lot and multi-variety workpieces and products.
Technical features
1.Hollow oil-cooled screw
Three-axis fast moving 60m/min and standard hollow oil-cooled screw to maintain stable accuracy.
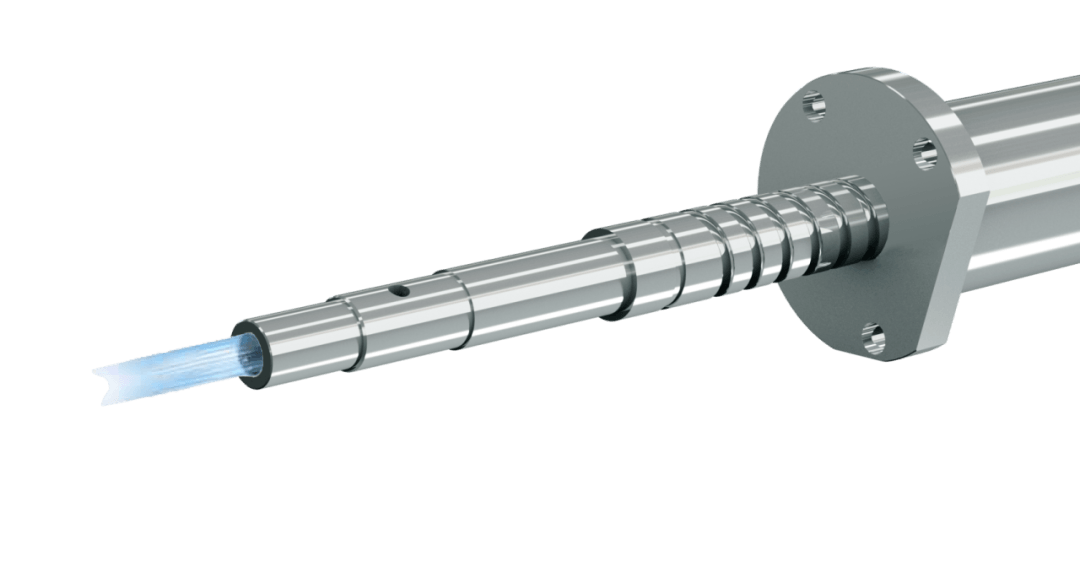
2.Built-in electric spindle for motor
Equipped with integral built-in electric spindle, which greatly reduces the vibration during running at high speed, and configured with synchronous oil cooling cycle technology to prevent thermal deformation and ensure stable cutting accuracy and finish.
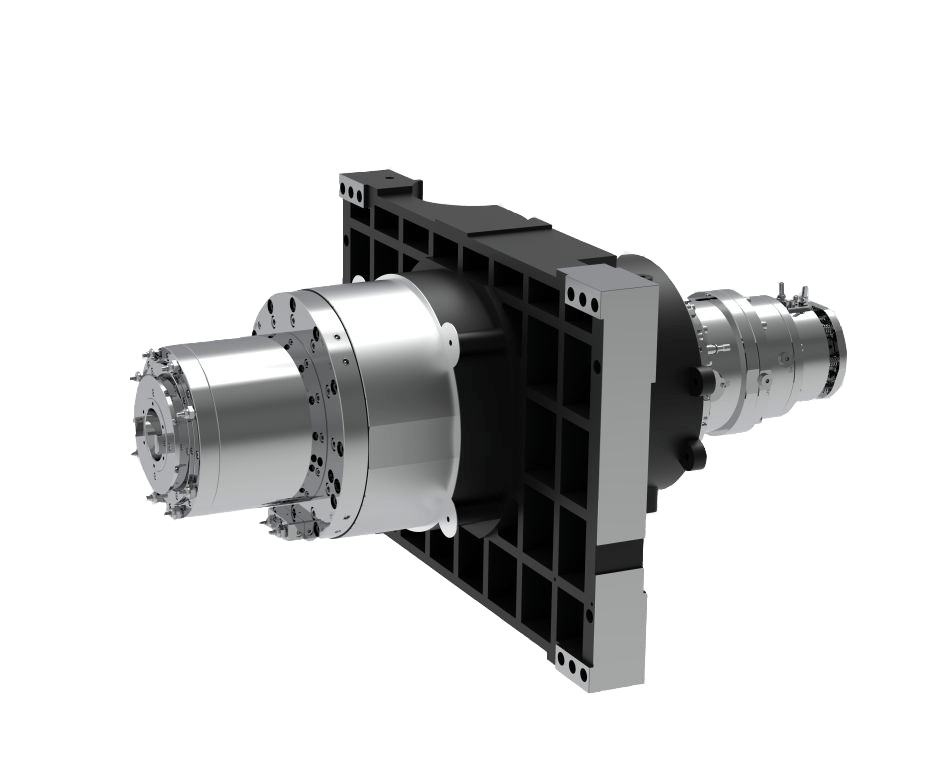
3.Servo-driven CNC turntable
B-axis CNC turntable with C-axis special turntable to realize BC-axis linkage five-axis machining function.
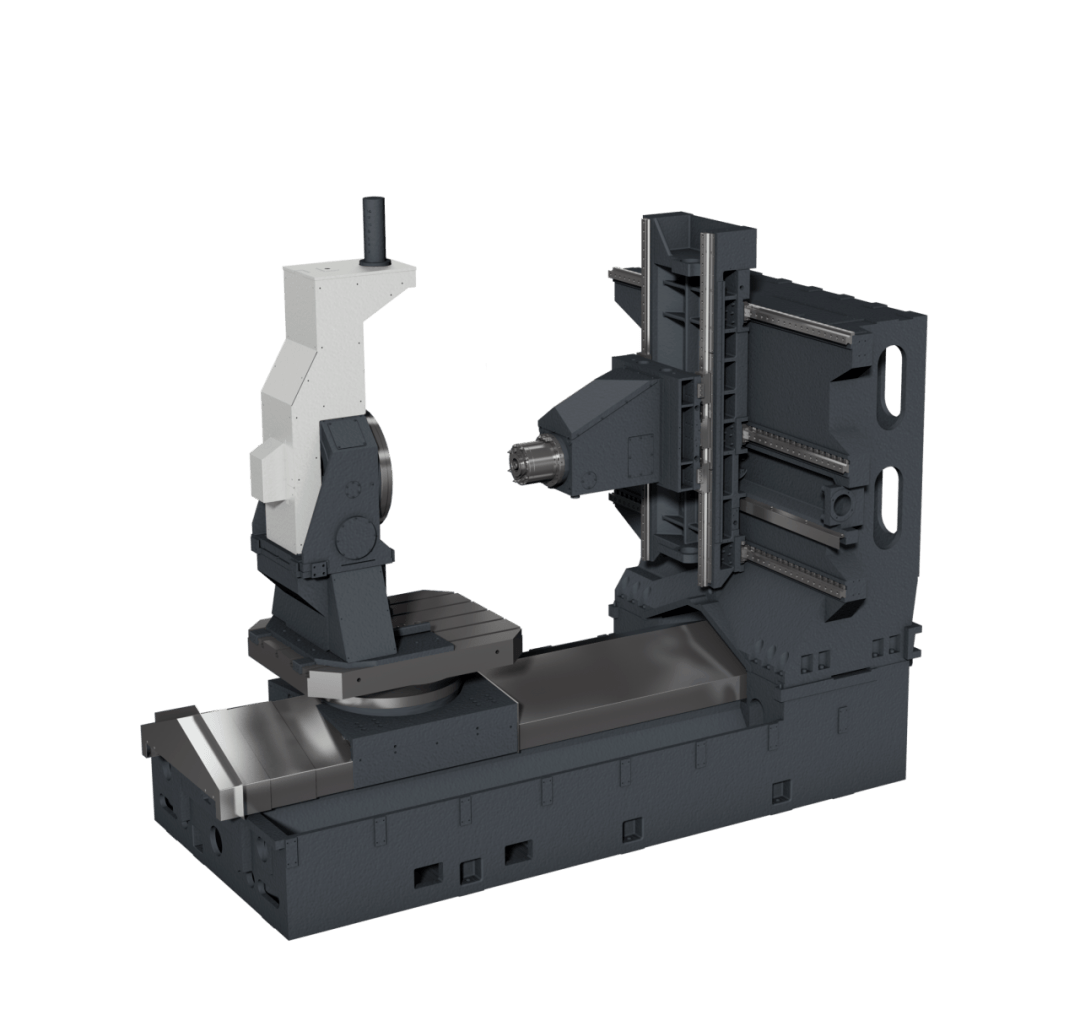
Machining cases
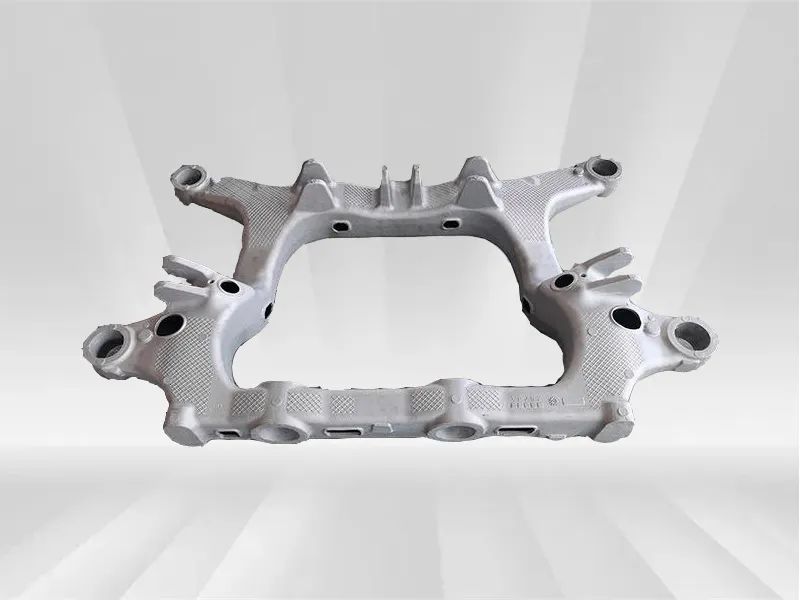
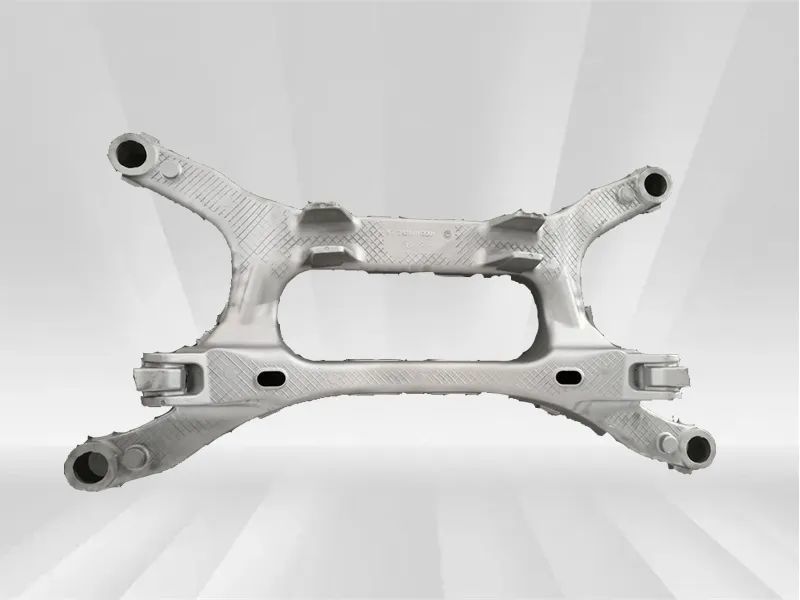